One of the most intriguing aspects of a watch is the dial. The dial, otherwise referred to as the face of the watch, is the first thing that most people notice. As such, this element bears a huge significance in the overall design and visual appeal of a timepiece. While there are multiple dial decorating techniques available, one that produces some of the most remarkable results is engraving. The art of engraving on watch dials is extremely hard to master. Throughout the years, watchmakers have perfected hand engraving, delivering designs that have stood the test of time. If you’re interested in learning more about engraving works, read on!
Tufina: mechanical Melbourne by Theorema Germany | GM-124-1 |
What is engraving?
Engraving is one of the most popular and complex decorative processes in watchmaking. In essence, engraving has to do with specific patterns and pictures that are carefully carved into the dial. However, this technique can also be applied on the case, the movement or other parts of the timepiece. In some cases, the watchmaker may choose to carve letters or numbers, which serves as a means of providing identification. Nowadays, watch manufacturers employ different kinds of engraving techniques and methods, from the most advanced to the artisanal ones.
How does engraving work?
Engraving is one of the most delicate processes in watchmaking. In order to engrave a dial, the watchmaker uses a very sharp tool to carve the metal from the dial (or the part of the watch that is being engraved). In this way, he creates the desired pattern. You’ll be able to find many designs that feature scrollwork or florals as some of the most popular motifs. Sometimes, engraving is used to create greater depth and dimension to the existing engraved motifs of a watch. It is important to mention that engraving is an extremely time-consuming process! One slight mistake can ruin hours and hours of work, as no errors can be retraced or fixed. For this reason, not many brands apply this technique and those who do, have usually passed down the craft from generations.
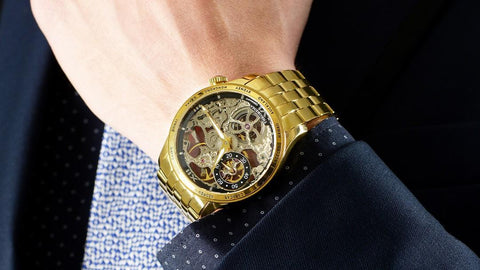
Tufina: skeleton Monte Carlo by Theorema, Germany.
What are the different types of engraving?
Engraving can be accomplished in one of two ways: either by hand or through the use of specialized machinery. Both methods are extremely intricate, and they have their own advantages.
Hand engraving
Incised engraving or otherwise known as intaglio is one of the most common forms of hand engraving. During this process, the watchmaker will cut into the watch’s metal using a burin. The watchmaker will first trace the pattern on the surface using a liner. Then, he will carefully incise the metal using the burin. An engraver can work with up to 20 different types of burins to achieve the exact shape and size of the patterns he is aiming for. As you can imagine, this process takes a lot of time to complete. Hand engraving must be extremely precise, thus it takes a lot of practice to master this technique.
Chasing
This technique is the opposite of engraving. During this process, the watchmaker creates a pattern by digging into the surrounding area. In other words, the pattern is created through relief. A beveled steel bade called a chisel is used to carry out this technique, which similarly to intaglio, is extremely difficult to master and very time-consuming.
Guillochage
This technique is a type of intaglio, and it has become a very popular method for decorating dials and cases. Dating back to the 16th century, Guillochage involves creating curved lines that interlace with each other. In order to create these very specific engravings, a Guillochage machine is used. This tool is made of a burin and a crank handle. Most watchmakers who are able to perform this technique pride themselves, as it is one of the most prestigious and complex methods in the industry.
Tufina Made in Germany Geneva Tourbillon by Pionier | GM-902-3 |
Damaskeening
If you’re interested in watches, you’ve probably heard of the term Geneva Stripes before. Geneva Stripes (Côtes de Genève) or Damaskeening refer to a very specific pattern found in high-end watches. This technique is often used to decorate plates, rotors and the visible parts of the bridges. The pattern showcases fine wavy lines that create an appearance similar to the waves of the sea. Damaskeening can be done by hand or through the use of a special digital-control machine. In either case, high precision is required for the successful completion of this very intricate technique.
Beading
Beading is a technique used to create very small circles close to one another. Sometimes, these circles can overlap. This method creates a matte effect. It can be done either by using quite expensive modern machines or by hand with a beading tool. Both methods create remarkable results that give timepieces a special aesthetic.
Modern engraving
Watch manufacturers may choose to invest in specialized equipment such as CNC machines. Although quite expensive, these technologies allow for the creation of beautiful engraved patterns that would otherwise take ages to achieve. Here are a few modern engraving techniques:
- Mechanical engraving: A CNC machine is used to carefully engrave special patterns, numbers or letters on movements. This tool allows for maximal precision and accuracy.
- Chemical etching: UV-sensitive protective varnish is used to cover the surface of the watch that will be engraved. Then, the watchmaker will position a negative of the design on top of the varnish. This negative is used to cover the parts that will be preserved. Then, the watch is exposed to UV rays before being dipped in a special acid agent. This allows for the erosion of the exposed metal, thereby creating the desired pattern. Chemical etching is most commonly used for the creation of extremely fine lines that can be a few tenths of a millimeter deep.
- Laser engraving: Similar to mechanical engraving, this technique makes use of a laser-controlled beam to create the desired pattern on the surface of the watch.
Tufina: Made in Germany San Francisco Theorema | GM-116-1 |
What are some other dial decorating methods?
There are quite a few other decorating methods used to create timepieces sought-after by watch admirers and collectors worldwide.
Latticework or skeletonizing
Thanks to the special appeal of skeleton watches, latticework has become more and more popular. This technique is used to cut out parts of the plates and bridges of a watch in order to create an opening through which the various components and gears can be shown. In turn, this openwork design takes the form of a pattern, quite often a floral one, creating a unique and special aesthetic.
Sunray brushing
Another popular decorating pattern would be sunray or spiral patterns. A dome-shaped grindstone is used to create these patterns. The result is a fine-line decorating that creates a hypnotizing look. When used on the barrels, barrel covers or the oscillating weight of the movement this technique is often referred to as snailing.
Final Notes
The art of engraving on watch dials dates back to centuries ago. A beautiful technique that showcases extreme precision, finesse and great attention to detail. As such, watch collectors and connoisseurs have developed a deep appreciation for this challenging craft. If you’re drawn to unique accessories and you want to see one of these engraved dial beauties from up close, we recommend you check out some of our skeleton timepieces. Our collections feature some amazing, hand-made watches with fine engravings on either their dials or movements!
Leave a comment